Ever wonder why you see so many U-Haul moving vehicles and U-Haul products when you’re out and about? It’s thanks to tools like the robotic arm in our AMFORM (American Fabricators of Raw Materials) factory in Glendale, Arizona. U-Haul is able to produce so many handy products for our customers in a short time because of AMFORM.
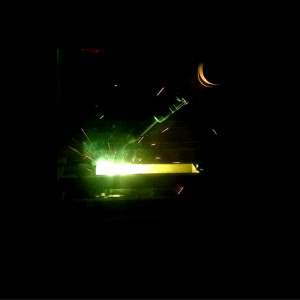
Caught in action: A robotic arm welds at AMFORM.
Pete Tolar, tooling supervisor, and Jerimy Pickrel, production supervisor at AMFORM, explain how the facility’s six cells of manipulators, what we call “robotic arms”, help produce various American-made U-Haul parts.
Sparks really do fly around the AMFORM facility–but some are from human welders, while others are from robotic arms programmed to weld precise metal parts together.
It’s a productive system–allowing the machines to automatically carry out welding projects in bulk, while still requiring the help of Team U-Haul to perform tune-ups and programming on the machines for extra precision.
Pickrel used a small touch-screen computer to initiate movement in one of the factory’s robotic arms. Just behind that manipulator cell, another U-Haul team member used another robotic arm to weld the frame of a utility dolly–sans wheels and orange paint coat.
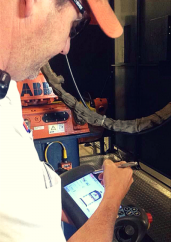
Jerimy Pickrel, production supervisor, programs movements for the robotic arm.
These robotic arms are programmed to weld the parts that make up dollies, axles and surge brakes, for the most part. Of course, these ABB-brand robotic arms require double-checking by U-Haul AMFORM team members to ensure quality on every single part made, but they absolutely make the production process much more efficient.
“They’re 10 times faster than a person is, and they come to work every day,” Tolar added with a laugh.
The six manipulator cells in AMFORM contain either single-arm robots or double-arm robots–each of which can be programmed to perform a separate function.
“We’ll program points for the robot to weld, to tell it where exactly to weld,” said Pickrel.
Around the AMFORM factory, many team members weld parts by hand, which helps ensure precision in tricky areas for the robotic arm.
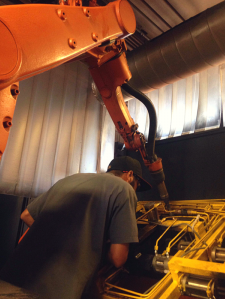
Team U-Haul member Ruben checks up on maintenance work for one of the robotic arms.
“There is maintenance on the robots, because they don’t know how to weld in certain spots,” Tolar added.
From raw materials carted into AMFORM to final, polished products ready to make U-Haul customers’ on-the-go lives more efficient, the tech center’s goals are reached in a timely manner thanks to their dedicated team members–including the ones made of metal!
Whether you’re using a utility dolly to take strain off your arms and back or attaching your trailer‘s surge brakes to your hitch and heading for adventure, don’t forget these pieces were made in America and crafted by robots!
Do you have a “Made in America” U-Haul story? Let us know in the comments below!